Hydraulic system self-propelled field sprayer
This unique pump set consists of a Linde HPV closed system pump to drive four Linde HMV wheel motors mounted directly on the wheel end reducers. Behind the first pump are two more Linde HPR open circuit pumps. These provide hydraulic wheel steering, spray pump drive and control of all cylinder functions on the boom, among other things.
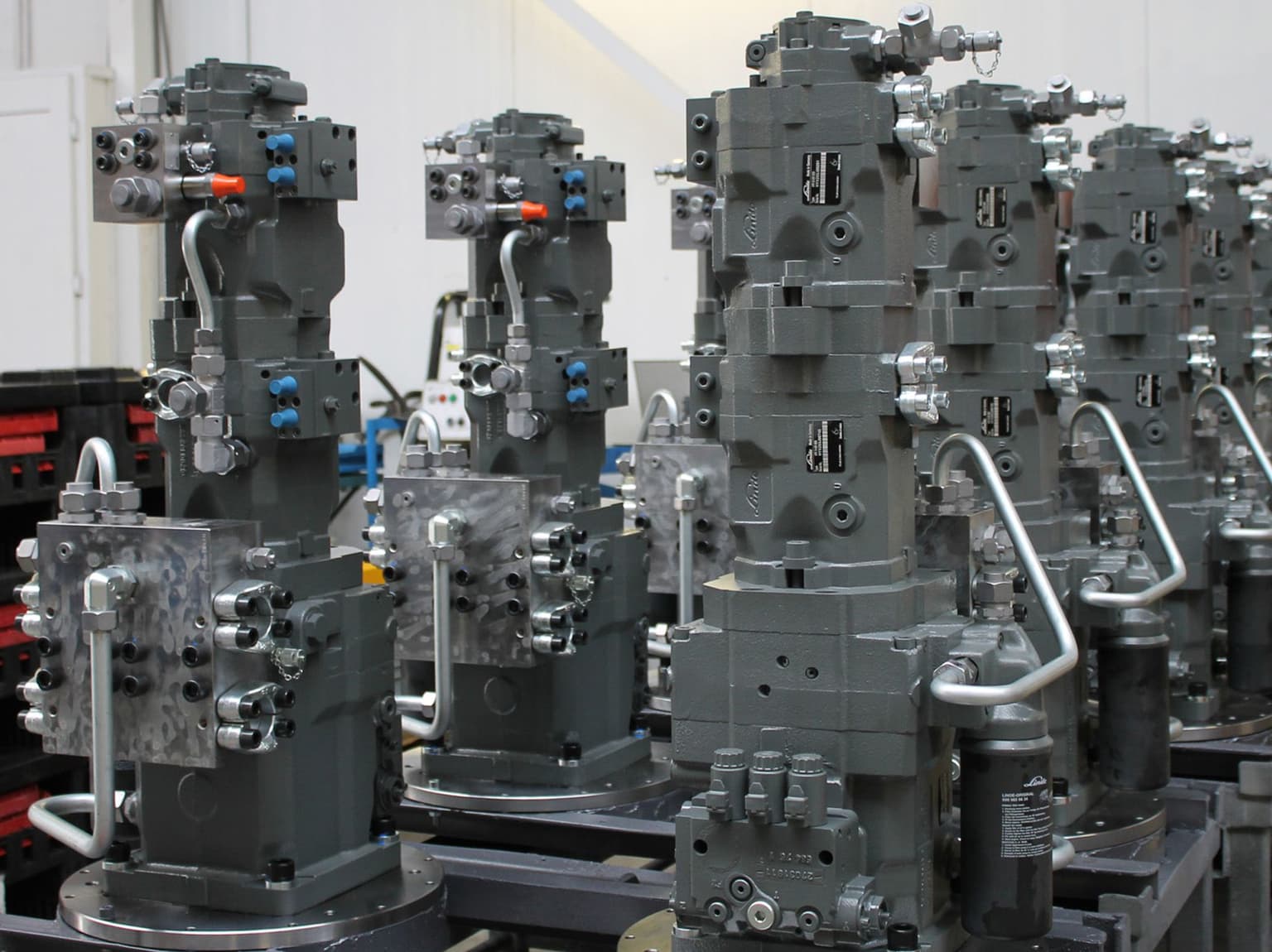
More about this project
The wheel motors are adjustable in stroke volume and have speed sensors which measure and influence the amount of traction per wheel as well as the speed. A Völkel travel controller regulates both the stroke volume of the pump and the hydraulic motors. Ideal for a large infinitely variable speed range, traction control in the field and anti-lock braking when braking on the road.
More projects
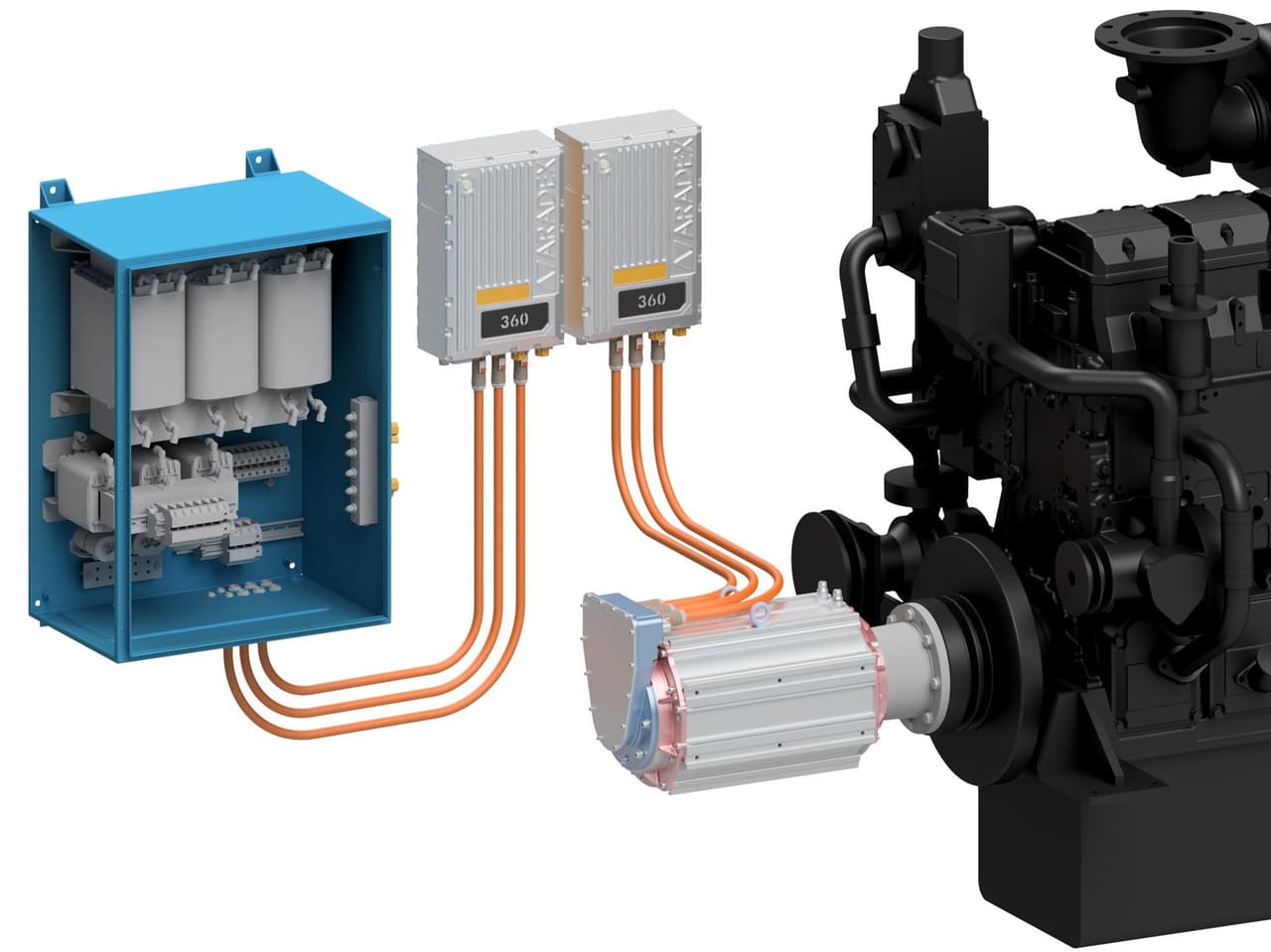
Electric shaft generator
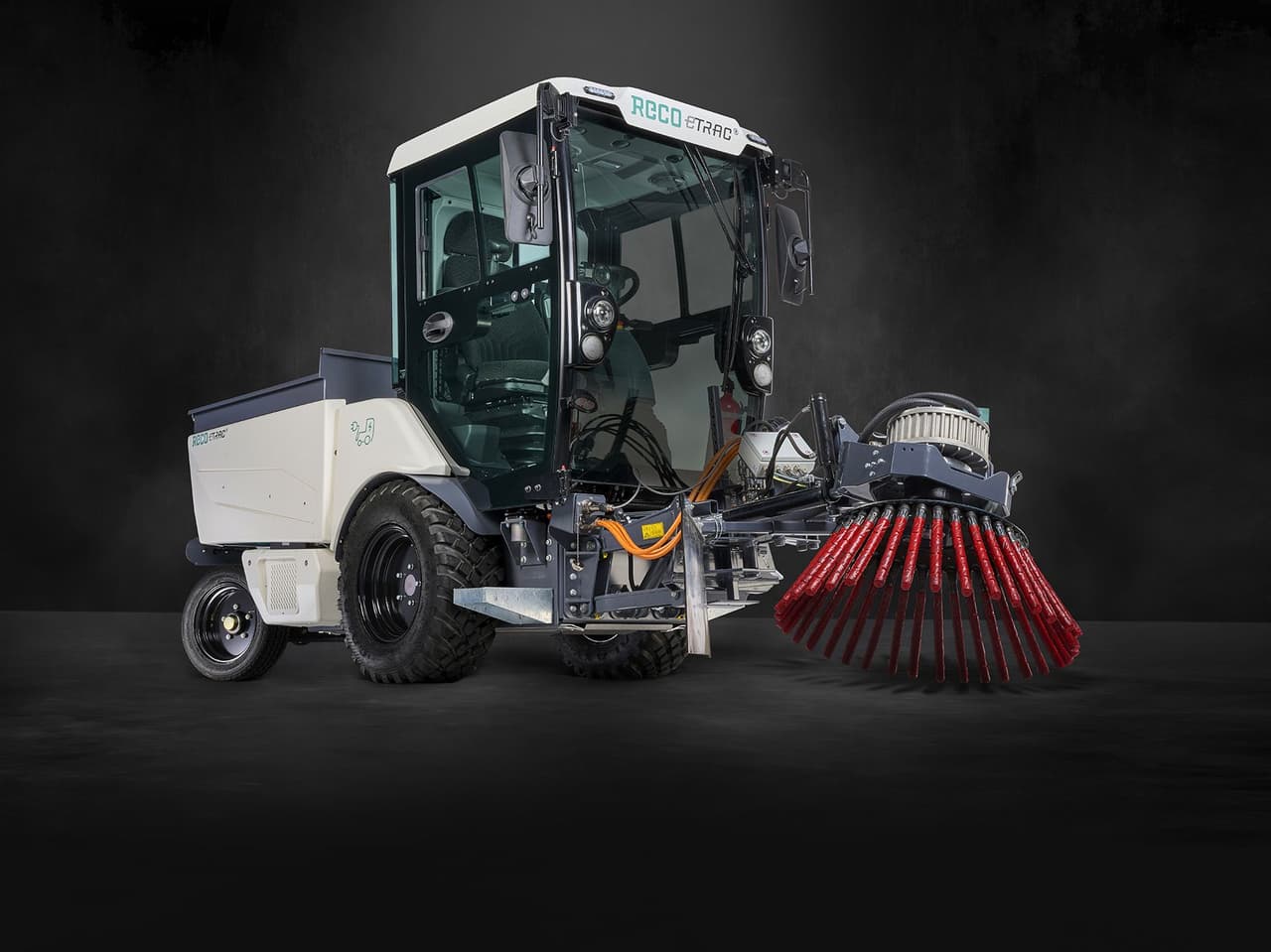
RECO eTrac electric tool carrier
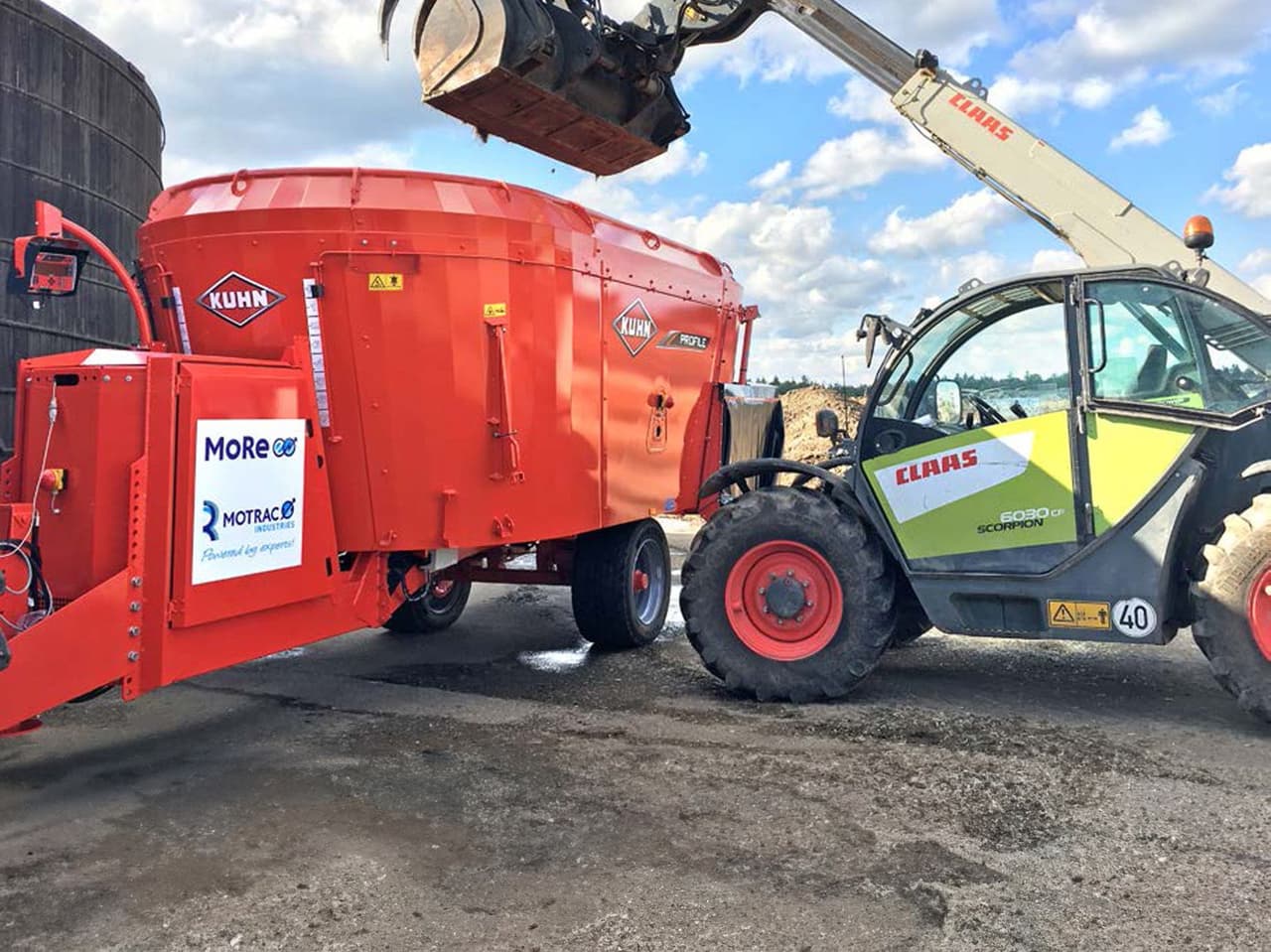